The planks are fitted by drilling holes at 200mm intervals (closer when the plank goes through at tight curve) and stitching the planks together with wire.
|
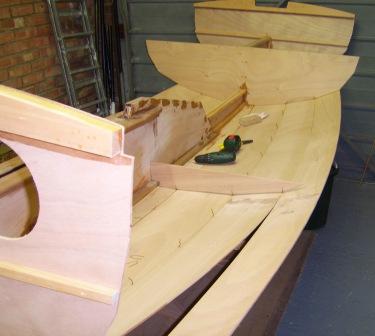
|
The planks are nailed to the frames - I found annular ring-gripfast nails good for this as they grip the ply.
That said I can count the number of nails I have ever hammered in straight on the fingers of one badly mutilated hand (whose digits were lost to misdirected hammer blows).
Hammering nails though 6mm ply in a compound curve into the end grain of 6mm ply leaves little margin for error.
I found the tension in the ply around frame A too strong for the nails and fitted temporary fillets.
|
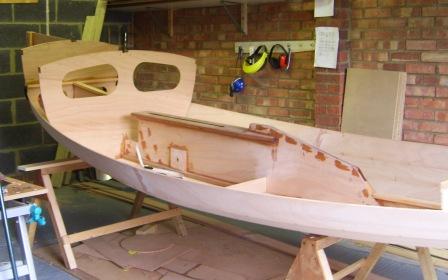 |
The planks are pulled together by twisting the wire stitches. Where one plank sits higher than the other putting a piece of dowel against the join in the planks and tightening the wire tie over the dowel will pull the planks into line.
|
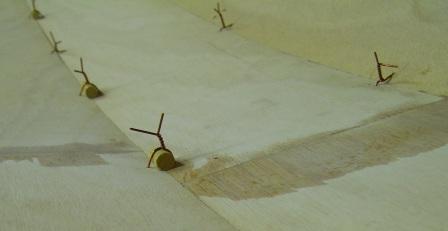 |
The centre structure has quite a lot of flex in it, which decreases as more planks are fitted.
I frequently sighted along the frames to check for twists and used a surveryors tape measure to check distances from the bow to the frames.
The bow fillets were planed and rasped to fit the curve of the planks.
When fitting these the far sighted boat builders amongst you will have placed the screws well back from the bow and out of the way of the section to be planed.
|
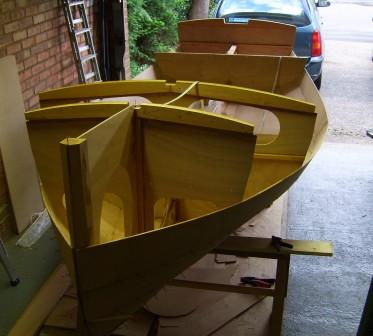 |
Finally everything is boat shaped which is a relief as the scope for making distastrous errors is more limited in the remainder of the build.
The planks were unscrewed from the bow fillets and then glued and screwed in place and also glued and screwed into the transom.
|
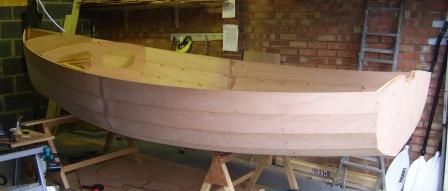 |
The joins between planks were primed with unthickened exoxy, then thickened epoxy was applied, inside and out, leaving gaps around the wire ties. Once this had cured the wire ties were removed.
The epoxy joins were sanded and then taped with glass tape and epoxy. Thickened epoxy fillets were applied between the frames and the planks.
|
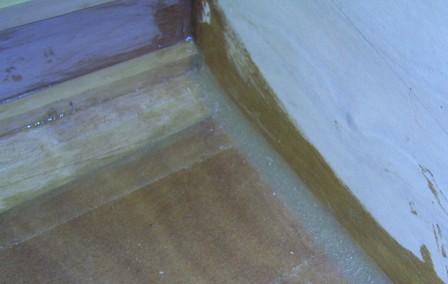 |
A large thickened epoxy fillet was applied between the planks and the transom. This fillet was strengthened with glass tape.
|
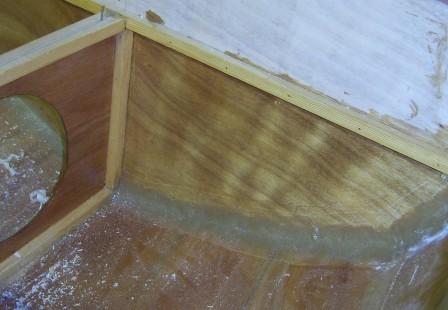 |
The boat didn't seem that heavy so the turnover team consisted of 2 turners and one photographer.
It was easy to turn the boat to 90 degrees at which point the photographer's help was quickly enlisted as the centre of gravity
was stopping us from turning the boat through the vertical. More hands will be recruited for the next turnover.
|
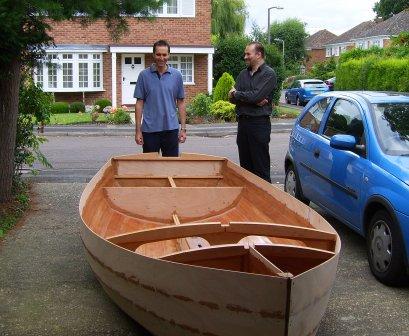 |
The epoxy joins on the outside of the hull were sanded. The bottom 3 chines were sheathed in glass mat to protect
the hull when hauled out on a beach. The remaining seams were taped.
|
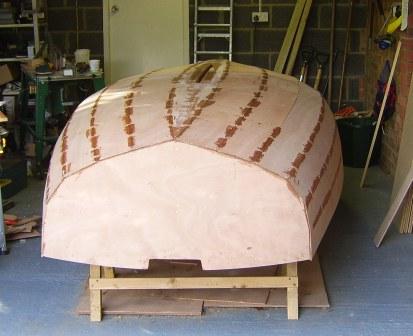 |
I had read accounts of sheathing going wrong on peoples projects so was wary of this stage. This was my last chance to ruin the boat.
I used glass mat and epoxy from Fyne Boat Kits as they supply kits so I reasoned their materials must be good for an inexperienced builder.
Glass mat was draped over the hull and smoothed by hand. The centreboard slot was cut in it and it was cut roughly to size at the transom.
With hindsight it might have been better to cut along its length so it overlapped plank joins completely or not at all making subsequent taping easier.
A single cut along its length at the bow was all that was needed to get the fabric to drape over the curve of the hull without creases.
|
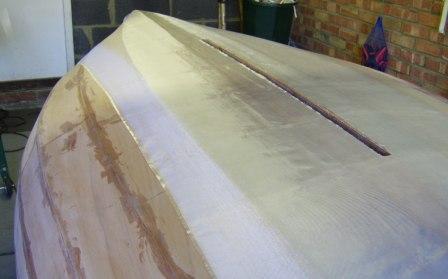 |
The cloth was wetted out on a warm day with epoxy warmed in a bowl of water. The epoxy ran like water and was
spread into the cloth using a squeegee. As I worked it became easier, there is a way of working with glass and epoxy,
the right amount of epoxy and the right amount of pressure with the squeegee. When cured the overhanging fabric at the bow and transom was cut with a knife.
|
|
There were a few small air bubbles, these were removed with a paddle roller.
As I got the hang of working with the materials I used the paddle roller less and less.
During the afternoon the sun moved round to shine on the garage door warming the garage.
This encouraged the bubbles to reform and some had to be rolled out again.
On my next build I will choose a cloudy day so the garage does not change temperature rapidly.
If I had been building in cedar strip the results would be good enough to varnish - a good result.
|
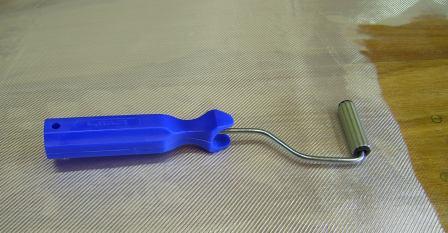 |